I recently put together what is basically a small UPS. It’s simple, made up of three diodes and some resistors, and lets you trickle charge a battery while power something and then seamlessly switch to the battery if the power source goes out.
This was actually built just for charging a small lithium iron phosphate (LiFEPO4) battery from a car cigarette lighter plug while power something, but it could be used for a lot of things. Here’s the schematic:
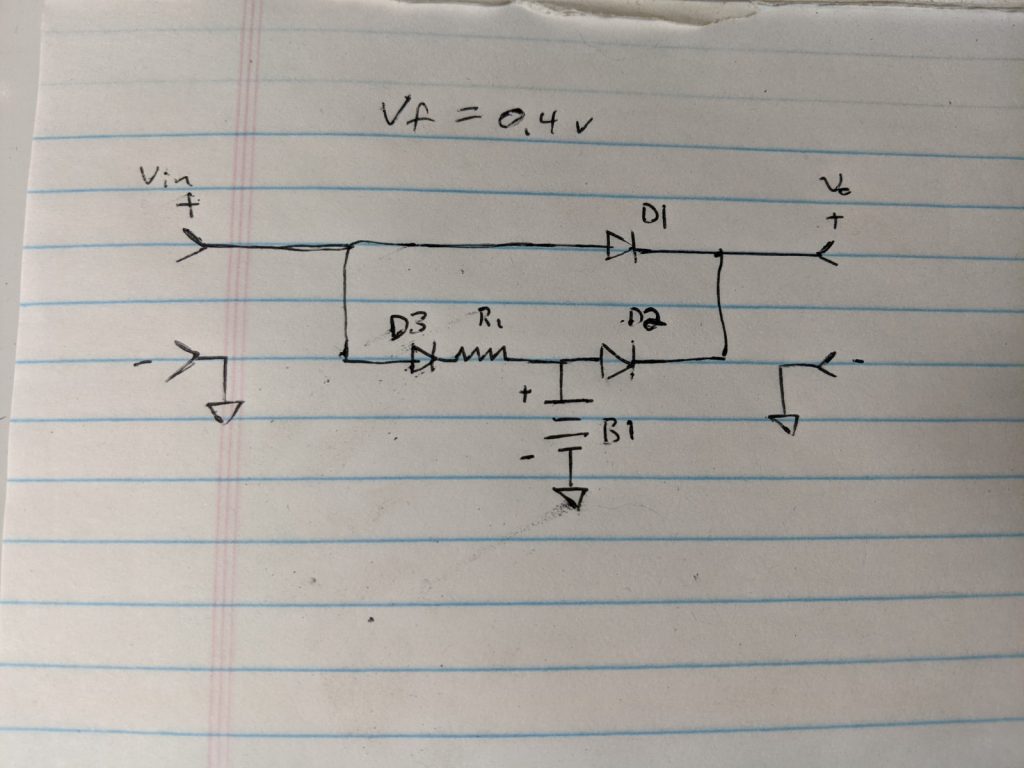
Basically, current can flow from the input to the output (Vin to Vo) through D1, or from the battery to the output through D2. If power is present, the battery can be charged through D3 and R1 – R1 sets the current, based on the voltage difference between the source and the battery, and the forward drop in D3.
This type of circuit is great because it’s simple, and it accomplishes a lot of what you’d like: it lets a source power something and trickle charge a battery, and switches the load to the battery if the source drops. It’s passive, and should just work. On the other hand, the battery is being passively charged, and it kind of relies on the voltage of the source to regulate it. There’s also the diode drops, which for a Schottky diode is around 0.4 V. For a normal silicon diode, it would be higher, around 0.7 V.
You could improve this with an ideal diode circuit, where you could basically control a MOSFET in place of each diode to turn on and off when the diode would. This is more complex, but you almost eliminate the diode drop. If you needed something like this to handle more than a few amps, that’s probably not a bad idea.
Another option, and probably the ideal one, is to use a power converter, at least to charge the battery. A non-inverting buck-boost converter would do this, and allow you to control the charging current regardless of the voltage of the source and B1. You could have it do a proper charge of the battery, bulk/absorb/float for lead acid, or bulk/absorb for LiFEPO4 (or whatever scheme that battery chemistry calls for). A fancier converter (or converters) might supply a constant voltage to the load at the same time.
Still, for something small, the simplicity here is nice. It could work well for something like holding up a Raspberry Pi or other single board computer, for instance. One thing to note is that most diodes in a TO-220 or TO-240 or similar case often are not electrically isolated. You can get a heat sink with an electrically insulating thermal pad; I have one I garbage picked a while back.
Here is what the circuit looks like, assembled:
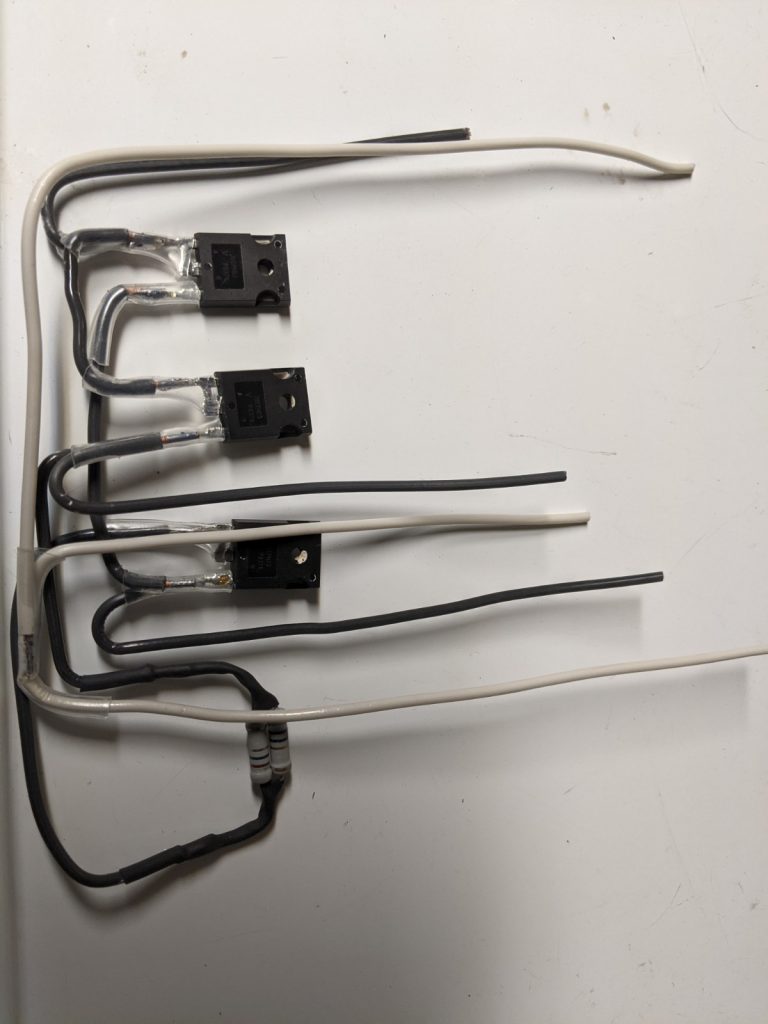
I put it in a heat sink and attached some leads with Anderson Powerpole connectors, like the following:
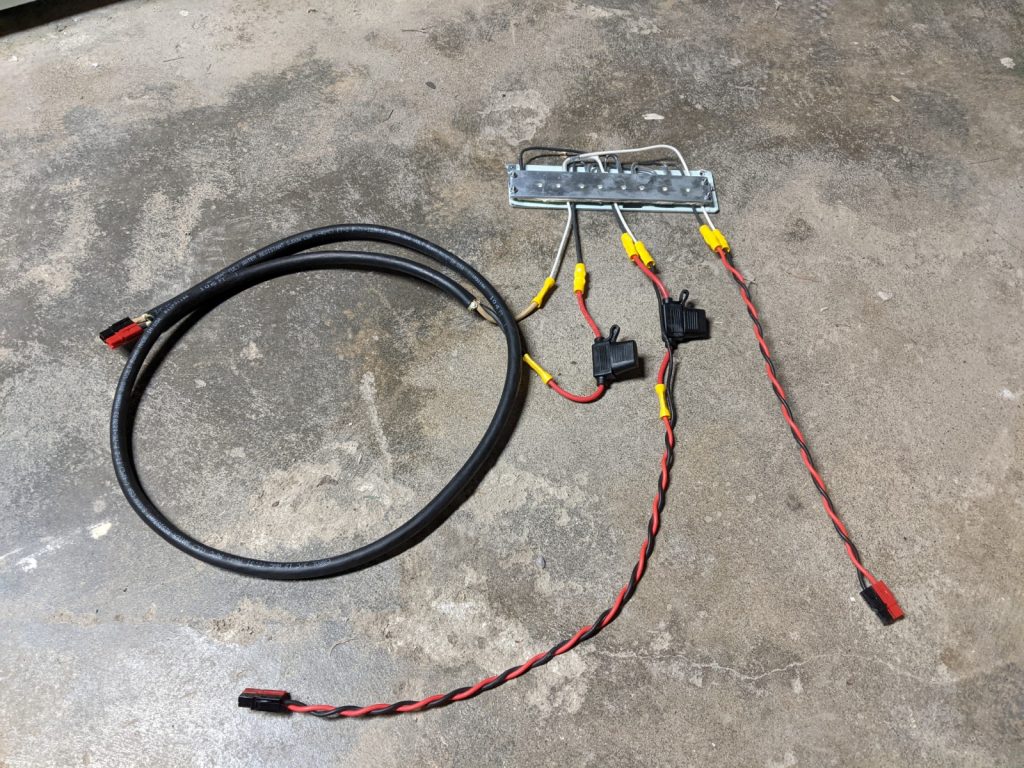
Note that I did alter the resistors to get a little more charging current. The pictures show two 2.2 ohm resistors in parallel (for 1.1 ohms), but I added two 0.9 ohm resistors in parallel as well, for about 0.32 ohms total. The diodes have about a 0.6 V drop under load, so from my car I was able to get around 1.75 amps into a LiFEPO4 battery, while the car is running. This will vary a little, and keep in mind that if your battery is at a lower state of charge you’ll get more current initially.